Уральские ученые нашли замену импортному оборудованию на заводах

В Российском государственном профессионально-педагогическом университете создали высокоэффективные плазмотроны для резки металла. По характеристикам они ничуть не хуже зарубежного оборудования, зато в несколько раз дешевле.
По словам руководителя проекта — заведующего кафедрой математических и естественнонаучных дисциплин, кандидата физико-математических наук Сергея Анахова, разработкой уже заинтересовались представители нескольких компаний. Как рассказал URA.RU ученый, уже в следующем году оборудование могут запустить в массовое производство.
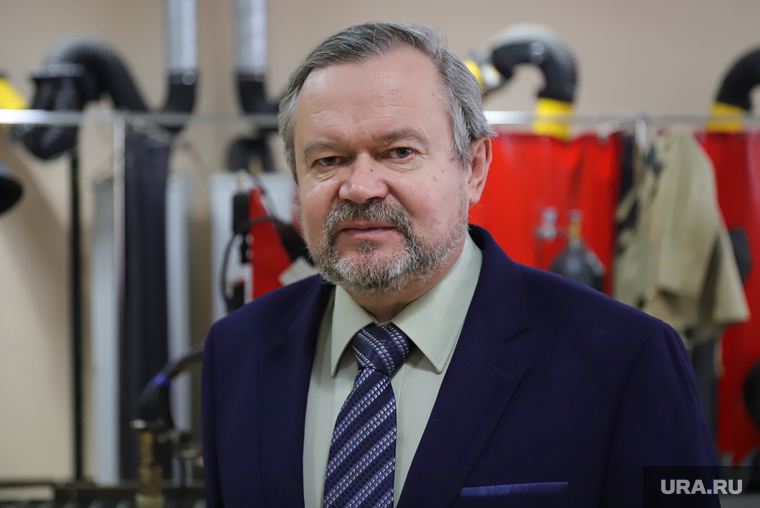
— Для начала давайте расскажем, что такое плазмотрон?
— Плазмотрон — это генератор низкотемпературной плазмы. Принцип его работы таков: внутрь устройства подается плазмообразующий газ, по газовоздушному тракту он попадает в сопловой узел, где происходит возбуждение (в нашем случае это происходит с помощью метода высокочастотного пробоя) и газодинамическая стабилизация электрической дуги, а также сжатие газа плазмообразующего газа, затем электрическую дугу выдувает из сопла, и получается высококонцентрированный поток низкотемпературной плазмы.
Температура плазмы в плазмотронах доходит до 20 тысяч градусов. Для понимания: температура плазмы в солнечной короне — порядка миллиона градусов. И вот эта горячая плазма выдувается со скоростью несколько сот метров в секунду, и металл фактически расплавляется и выдувается.
Таким образом можно резать металл качественно и быстро — всего за несколько секунд. Если делать это механическим способом, то уйдут минуты. Есть еще лазерная резка, гидроабразивная резка, но все это очень дорого, есть также газовая резка, но она менее качественная. По соотношению скорости, качества и энергозатрат именно плазменная резка считается наиболее эффективной.
— Ваш плазмотрон сможет заменить импортное оборудование на заводах?
— Да, наше оборудование будет актуально для трубных, машиностроительных, оборонных заводов, плазмотроны используются на предприятиях корпорации «Ростех», в «Объединенной судостроительной корпорации». Сейчас там в основном режут металл с помощью плазмотронов, произведенных в США, Германии, Швеции. Но в связи с серьезным удорожанием продукции, а также из-за проблем с поставками, появляется задача импортозамещения. А то, что предлагают отечественные разработчики, — это по большей части достаточно устаревшая продукция.
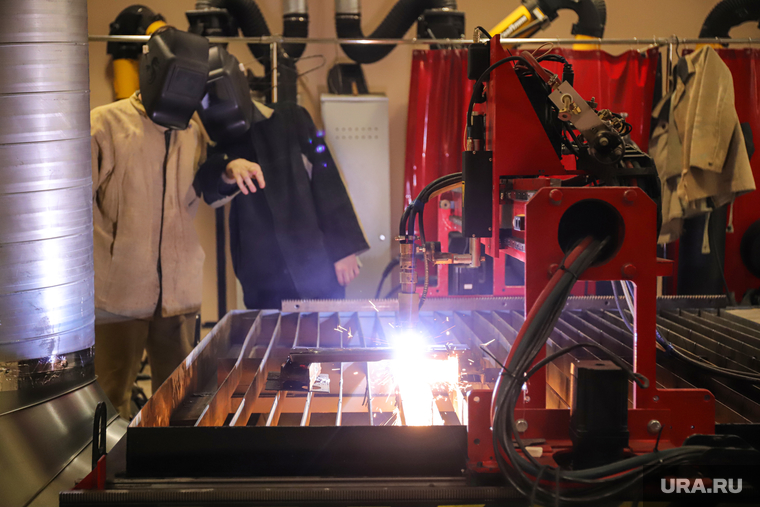
— Почему так?
— В 1980—1990-е годы проводились достаточно серьезные исследования в этой сфере. Тогда перед учеными стояла острая проблема создания плазмотронов для оборонной промышленности, они нужны были также для предприятий трубной, нефтегазовой промышленности. Необходимо было внедрить максимально простой плазмотрон, без использования дорогостоящего газа, чтобы он был надежен и долговечен. И ученые его разработали в 1990-е годы. Но потом появились зарубежные технологии, которые достаточно быстро завоевали рынок. Так что сейчас нам приходится завоевывать рынок заново. То, что мы делаем, я считаю, является действительно прорывным и может сыграть важную роль в политике импортозамещения. Плазмотроны, который мы разработали, сопоставимы по своим характеристикам с зарубежными технологиями, разве что по дизайну мы немного уступаем.
Фактически инициатор плазменной тематики у нас на Урале — это Юрий Анатольевич Пыкин. Он привлек меня к этой проблеме, и по сей день мы ей занимаемся. Он является гендиректором НПО «Полигон», который и производит плазмотроны, а я являюсь руководителем научных программ. Хотелось бы еще отметить важную роль в проекте доцента УрФУ Анатолия Владимировича Матушкина (мы сотрудничаем не только с вузами Екатеринбурга, но и с институтами УрО РАН).
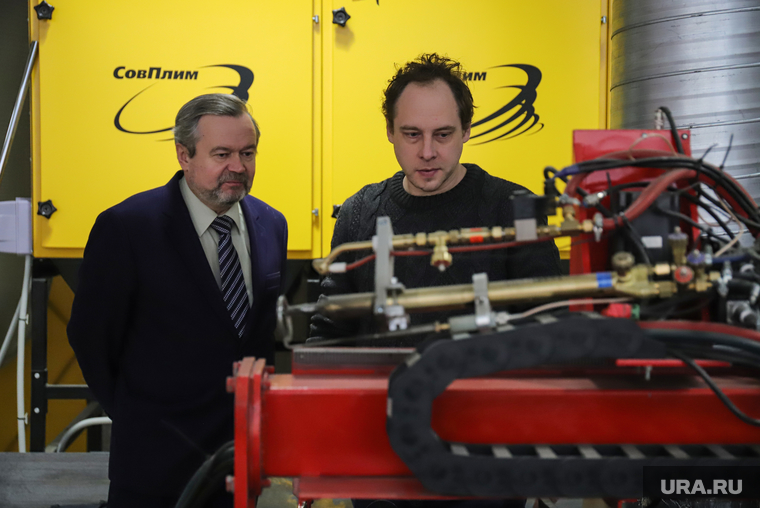
— Вы сказали, что зарубежные плазмотроны сейчас сильно подорожали, а наши технологии для заводов будут более доступны?
— На днях я узнал, что мы выиграли грант, и в рамках него нам положено 100 тысяч рублей на покупку высокоэффективного импортного плазмотрона. Он нам необходим, чтобы можно было его подключить, посмотреть, какое у него качество резки, сравнить характеристики с нашим плазмотроном. Сейчас мы посмотрели цены, и оказалось, что 100 тысяч, на которые мы рассчитывали приобрести плазмотрон, уже недостаточно. Цены сейчас существенно возросли. Мы же свои плазмотроны продаем за 50-60 тысяч рублей, то есть в несколько раз дешевле.
— На каких-то предприятиях вашу разработку уже внедрили?
— Наши плазмотроны используются на Синарском, Волжском трубных заводах. Проявили интерес АО «ПО «Севмаш», АО «Автоваз». Мы сейчас также ведем переговоры с ОАО «РЖД» — у них много структур, которые занимаются ремонтом подвижных путей, локомотивов, а это металлопроизводство и, соответственно, различные формы плазменной резки.
— Ожидаете еще большего всплеска интереса со стороны бизнеса?
— Я думаю, что 2023 год будет переломным в этом отношении. Пока у бизнеса еще есть ресурсы, есть старые запасы импортных плазмотронов.
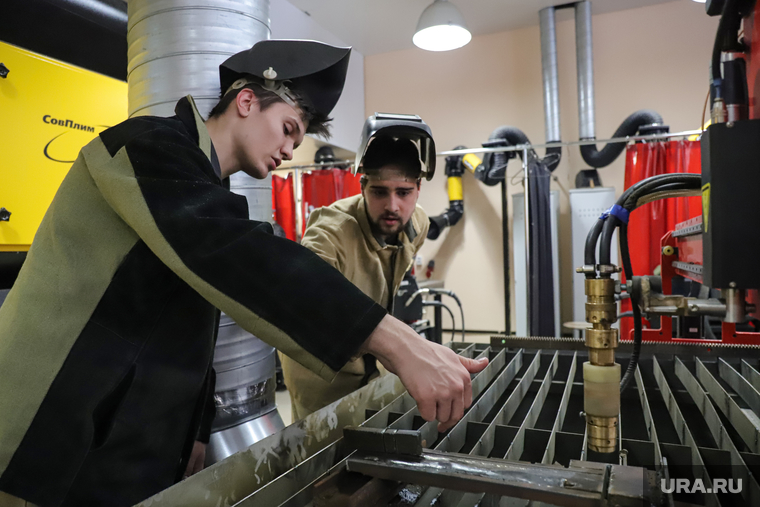
— Помимо резки металла, для чего еще могут применяться плазмотроны? И работаете ли вы в других направлениях?
— Да, параллельно мы еще занимаемся экологической тематикой. Плазмотроны также можно использовать для обезвреживания путем дожигания различных токсичных газов. У нас уже есть такие опытные модели, разработанные в рамках недавно реализованного гранта РФФИ, но внедрение этих технологий — непростая задача. Это связано с тем, что для таких проектов обычно нужна государственная поддержка, бизнесу они не сильно интересны, поскольку прибыли не приносят, разве что косвенно — в виде снижения штрафов.
— Где именно используются технологии обезвреживания?
— Например, в рамках национального проекта «Экология» сейчас строится четыре завода по термическому обезвреживанию отходов. Там применяются технологии японской фирмы «Хитачи». Стоимость каждого завода — более миллиарда рублей, и основная доля затрат идет именно на обезвреживание образуемых выбросов. Так вот, чтобы удешевить проекты, мы предлагаем использовать на стадии дожигания токсичных газов наши технологии.
Что касается других разработок, то у нас есть опыт в технологиях плазменного термоупрочнения (с помощью этих технологий можно закаливать различные поверхности), технологиях плазменного напыления (наращивания металла на изношенных рельсах, колесах), технологиях утилизации металлоотходов. Мы создавали мобильные установки, с помощью которых можно было на месте разрезать различные объекты (танки, суда, самолеты и т. д.) в транспортный габарит для их утилизации или последующей переработки.
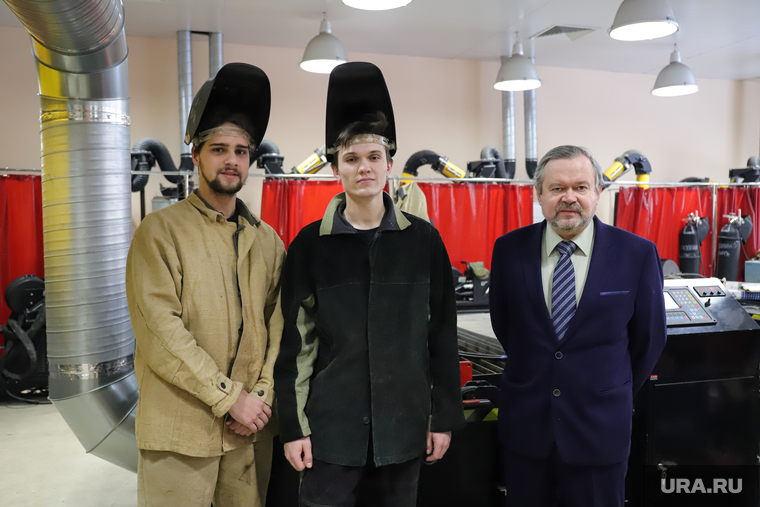
— Студенты РГППУ тоже участвуют в разработках? Будет кому продолжить ваши начинания?
— Когда у нас появилась база для исследований, мы начали новые технологии активно внедрять в учебный процесс. Несколько лет назад мы создали новую образовательную программу «Высокотехнологические процессы в плазменном и сварочном производствах». При поддержке и. о. ректора Валерия Васильевича Дубицкого были запущены новые программы.
В следующем году мы запустим еще одну новую программу «Высокоэнергетические процессы и технологии в машиностроении и материалообработке». Там студенты будут обучаться и плазменным, и лазерным, и электронно-лучевым, и другим методам обработки материалов. Это будет такая уникальная, комплексная программа, после которой у выпускников будут широкие возможности для трудоустройства.
У нас есть сейчас студенты, которых мы привлекаем к технологической части исследований. Надеемся, что в дальнейшем их число возрастет, а, кто-то, я надеюсь, займется и более глубокой научной деятельностью. Буквально на днях мы выиграли грант РНФ на исследования, обосновывающие эффективность применения наших плазмотронов в сварочных технологиях, и помощь молодых ученых нам, безусловно, потребуется.
Сохрани номер URA.RU - сообщи новость первым!
Не упустите шанс быть в числе первых, кто узнает о главных новостях России и мира! Присоединяйтесь к подписчикам telegram-канала URA.RU и всегда оставайтесь в курсе событий. Подписаться на URA.RU.
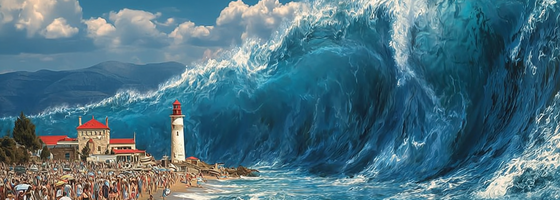